Human ingenuity for storing written communication has always been high. What started on cave walls quickly became more portable as early people used clay, palm leaves, snake skins, tortoise shells, and other handy surfaces to store and share knowledge. However, the desire for a higher level of permanency beyond the cave wall eventually led from dried or fired clay to papyrus and paper.
The Development of Standard Paper
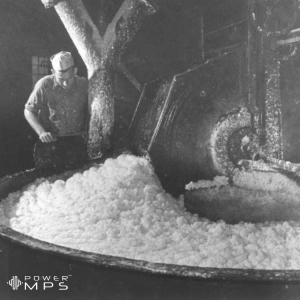
How they use to make paper
Anyone who has held handmade paper can immediately tell the difference from the now much more common store-bought notebook, school, or standard paper. The texture is slightly less even, and the surface is typically thicker and stiffer. The differences lie in the process.
Handmade paper is created by beating, or breaking apart, fibrous materials such as cotton, hemp, or old cloth into their individual strands. These strands are then saturated with water and filtered onto a screen. The wet sheet is then pressed to remove excess water and laid out or hung to dry. Once fully dry, the paper is pressed to flatten the sheet, then cut to the appropriate dimensions for use. In handmade papermaking, this size was usually determined by the widely used “Dutch” standard mold of 44” x 17”, which is cut down evenly to eight 8.5” x 11” pieces.
Today’s commercially available paper adds additional steps to the process, a transformation that began in the 1800s when soda and sulfite pulps were first manufactured from wood. A patent for sulfite pulp was issued in the United States in 1867 and, by 1875, paper production was industrialized.
These sizeable industrial production processes could efficiently pump out almost any paper size imaginable. However, in 1921 the Elimination of Waste in Industry program created by President Herbert Hoover launched the Committee on the Simplification of Paper Sizes. And, to not only eliminate waste but also help handmade paper companies in business, determined to require the standard Dutch sizing – and the official 8.5” x 11” letter was born.
Paper Becomes Smoother and Whiter
The whiter a piece of paper, the more easily the eye can view and distinguish the images and text inked on top of it. So, even before industrialization, whiter paper was a commodity. Before the invention of bleach, papermakers seeking to produce genuinely white paper made their sheets from fine white linen. If that was not available, a bluing agent was added to the water to correct muddiness. Today’s handmade papermakers use a variety of tactics, including newer options such as bleaching and vinegar.
Industrial papermakers benefit from using sulfite pulp rather than rags or other fibers containing additional color. This lack of color means that instead of adding an extra bleaching step to the process, they can add chalk to their mixture before grinding everything down to microfibers. In addition to whitening the resultant paper sheets, the chalk also fills in the gaps that make handmade paper feel courser.
But paper whiteness is not the only difference industrialization has brought to the paper industry. As the world has become more reliant on copying and printing, more efficient machinery has required paper to be smoother. In response, large-scale papermakers have added additional steps to their papermaking process.
Rather than delivering fibers directly from the beating vat to the screen, industrialized paper mills push fibers through a filtration system to clear out additional particles and ensure fibers are a standard size. This homogenous mixture is then forced to spray an even coating across the screens through a nozzle. The result is a smooth surface that can be dried and compressed to the smooth paper sheets required for print.
What do Paper Ratings Mean?
When searching for printing paper, it can often be confusing how many options are available. In addition to selecting the proper sizing (standard, legal, or tabloid), there are a variety of ratings, including brightness, opacity, and texture.
Paper brightness is a measurement of how well the surface reflects light. High brightness is usually a paper that appears whiter and provides heavier contrast between inked letters or images and the background. When making paper, the brightness can be adjusted using minerals and dyes during the pulping process. Printing paper usually comes with brightness ratings between 80 and 113, where the higher numbers are the brighter paper.
Printing Paper Texture
The texture of paper refers to how coarse the surface feels. The level of grain is fundamental when considering paper for laser or inkjet printing. Coarser printer paper is best for inkjet printing as the fibers can capture sprayed pigment and reduce bleeding. However, that same texture could interfere with the heating elements and toner bonding in a laser printer or copier. For laser printers, a smoother paper is more heat resistant and a better choice for more precise prints.
Opacity is a measurement of how well light penetrates the paper. For instance, a paper with a lower opacity would not be suitable for two-sided printing as light easily passes through and displays the ink from the opposite side. Standard 20# copy paper is lower opacity and not recommended for double-sided printing. Opacity is determined by a combination of the brightness and thickness of the paper. Higher brightness and pound ratings will provide lower opacity.
Without the industrialization and development of paper, the digital age would look very different. Fortunately, paper manufacturers have risen to the challenge, developing a wide range of paper options to meet the demands of every office printing purpose and machine. While times have changed, printing paper is still in very high demand.